Fixed Deaerator
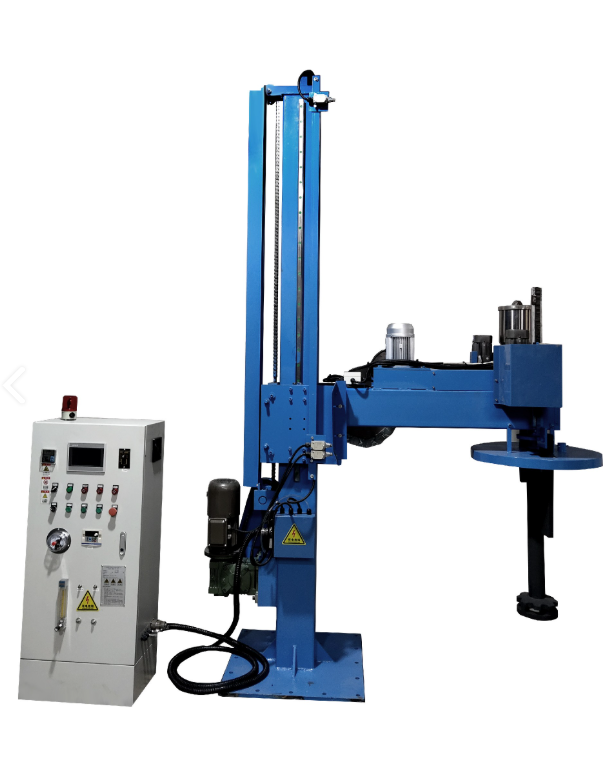
Basic Working Principle:
The degasser rotates on a fixed chassis, enabling the degassing head to service multiple furnaces. Degassing is achieved through a controlled rotating graphite shaft and rotor that stir the aluminum melt while injecting measured inert gas through the rotor. The gas is dispersed into microscopic bubbles evenly distributed within the molten metal. With a gas partial pressure of zero in the bubbles and a higher hydrogen partial pressure in the aluminum melt, hydrogen continuously diffuses into the bubbles. Simultaneously, non-metallic inclusions in the melt adhere to the bubble surfaces. Useless hydrogen and inclusions attach to the inert gas bubbles, which rise to the surface, achieving degassing and purification of the aluminum melt.
Features of the Fixed Rotary Degasser:
A. Single Inert Gas System:
A single inert gas is injected via the rotor and fragmented into tiny bubbles evenly dispersed in the molten metal. With zero gas partial pressure in the bubbles and higher partial pressure in the aluminum, larger bubbles form as hydrogen and inclusions adhere to the bubble surfaces. These bubbles rise to the surface, enabling hydrogen removal and oxidation inclusion purification through skimming.
B. PLC Control with Touchscreen Interface:
Equipped with a PLC programmable controller and touchscreen display, the system supports manual and automatic operation, multiple fault alerts, and fully automated workflows. This reduces labor intensity, minimizes human error, and ensures operational safety.
C. Adjustable Parameters:
Degassing time, speed, rotation, elevation, descent delays, and other settings are programmable.
D. Automated Workflow:
The system sequentially executes gas injection, rotation, degassing, rotation completion, elevation, and gas cutoff. Customizable actions are available per user requirements, optimizing inert gas consumption and preventing graphite rotor blockages.
E. High-Performance Guide Rails:
Durable, oxidation-resistant precision guide rails ensure smooth vertical motion. The integrated head and chassis design reduces vibration and swing during operation, extending graphite rotor lifespan.
F. Oxidation-Resistant Graphite Components:
High-temperature-treated graphite rotors and discs enhance durability, reducing operational costs for users.
Manufacturing Process of the Fixed Rotary Degasser:
A. Frame and Materials:
- Fixed Chassis: 18mm-thick steel plate (diameter: 800mm) reinforced with triangular gussets.
- Lifting Column: 200×200×5mm square tubing.
- Control Cabinet: Console-style enclosure (500×500×1700mm) with 1.2mm cold-rolled steel panels and powder-coated finish.
- Lifting Mechanism: 30×60mm steel beam with 6mm dual chains; 5# steel channel for the lifting head.
- Rotating Mechanism: High-strength plain bearings and large-diameter smooth shafts ensure stability and minimal clearance.
B. Fabrication:
- Welding: The chassis, columns, control cabinet frame, lifting chains, and head assemblies are welded, followed by grinding and polishing.
- Fastening: Bolts secure cabinet panels, motor mounts, and switches.
C. Lifting System:
Dual-chain and guide rail mechanisms enable stable vertical motion.
D. Surface Treatment:
- Chassis and Control Cabinet: Derusted, rust-proofed, and double-painted.
- Head and Cabinet Panels: Derusted, degreased, and powder-coated.
Technical Specifications (Customizable per Client Requirements):
- Frame Height:
- Maximum overall height: 3000mm (height adjustable per client specifications).
- Dual-station rotary design (expandable to 1–4 fixed stations at a uniform height, as per client requirements).
- Head Dimensions:
- Overall dimensions: Width 300mm × Length 1750mm × Height 300mm (length customizable).
- Head Travel:
- Vertical movement stroke: 1200mm (adjustable per client requirements).
- Graphite Rotor and Turntable:
- Maximum height above ground: 1650mm; minimum lowering height: 500mm (heights customizable).
- Furnace Compatibility:
- Suitable for furnaces with internal diameters ≤1600mm; minimum crucible inner diameter: 600mm.
- Lifting Baffle:
- Graphite baffle dimensions: 500×130×25mm.
- Power Supply:
- Three-phase 380V + N (neutral) line; three-core four-wire cable (3×2.5mm² + 1.5mm²).
- Signal Cable:
- Length: 6 meters.
This is a reference diagram, and each customer has significant differences depending on their environment and location. The specific agreement shall prevail, and physical delivery shall prevail.
Key Configuration Parameters and Manufacturers
Parameter | Description |
---|---|
Model | PLC |
Control Mode | Touch Screen (Siemens/Simatic) |
Adjustment Display | Chain Lifting System |
Inverter | Schneider Electric (1.5KW) |
Contactor | Schneider Electric |
Switch | Schneider Electric |
Overload Protection | Schneider Electric |
Relay | Omron |
Limit Switch | Hangzhou Shangkun |
Reducer | Turbo Reducer with Brake (Dedong Motor) |
Lifting Method | Dual-Chain System |
Rotor Lifting Stroke | 1000mm |
Rotor Ground Clearance | ≤1450mm (Customizable) |
Lifting Power | 0.75KW |
Rotor Motor | Dedong Motor (1.5KW, Variable Frequency Speed Control: 100–700 RPM) |
Arm Length | 1500mm |
Head Travel Stroke | 60–1700mm |
Head Travel Motor Power | 0.55KW (Aoqili Motor) |
Refiner Storage Capacity | 5KG |
Refiner Particle Size | ≤200 Mesh |
Refiner Feeding Motor | 270W (Aoqili Motor) |
Mobility | Manual Push |
Gas Type | Inert Gases (Argon, Nitrogen, etc.) |
Gas Flow Regulation | Flow Valve Control |
Gas Flow Range | 5–50 L/min |
Rotor Material | Graphite |
Rotor Dimensions | Length: 800mm, Diameter: 80mm |
Runner Dimensions | Diameter: 220mm |
Runner Material | Graphite |
Runner Runout Error | ≤0.05mm |
Baffle Material | Graphite |
Baffle Dimensions | 500×130×25mm |
Total Weight | Approx. 600kg |
Customization | - 800mm-Long Graphite Rotor - Auto-Lifting Graphite Baffle - Applicable for Furnace Diameters ≤1600mm - Automatic Powder Injection - Glass Rotor Flow Meter (Yinhuan Brand) |
Connection Thread | M75×6, Length: 80mm |
Rotor Speed | 200 RPM |
Leave Message Get Price