Spinal Pedicle Screw-Rod Compression Fatigue Tester
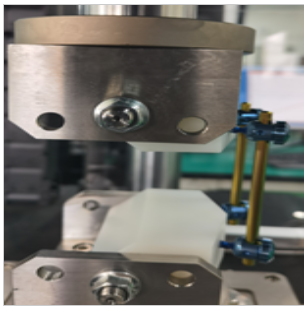
Standards:
ASTM F1717
ASTM F2706
ISO 12189
Main applications
Evaluating the fatigue life of spinal pedicle screw-rod systems with different materials and designs under compressive stress. By applying cyclic compressive loads, the tester determines how many cycles of compression the screw-rod system can withstand before fatigue failure occurs. This allows for the comparison of the fatigue resistance of systems made from different materials (e.g., titanium alloys, cobalt-chromium alloys), with varying screw designs (e.g., thread type, diameter, length), rod diameters, and connection mechanisms.
Studying the deformation, damage, and performance changes of spinal pedicle screw-rod systems under long-term loading. During prolonged cyclic compressive testing, the tester can monitor and quantify various aspects of the system's response, including axial deformation, potential screw loosening from the simulated bone, damage to the rod or connectors, and changes in the overall stiffness of the construct. This provides valuable insights into the degradation mechanisms under compressive fatigue.
Comparing the differences in compressive fatigue performance among spinal pedicle screw-rod systems from different brands and models. The tester provides a standardized and objective platform for comparing the compressive fatigue durability of commercially available spinal fixation systems.7 This data is crucial for surgeons, hospitals, and purchasing departments to make informed decisions based on the expected long-term mechanical performance of the implants.
Providing scientific evidence for the research, development, production, and quality control of spinal implants, and helping to improve and optimize product designs. The data generated from compression fatigue tests is essential for supporting the safety and efficacy claims of spinal pedicle screw-rod systems in regulatory submissions (e.g., to FDA or equivalent bodies). It also serves as a critical tool for R&D engineers to optimize implant designs, material selection, and manufacturing processes to enhance compressive fatigue resistance and improve clinical outcomes. Furthermore, it is used in quality control to ensure that manufactured systems consistently meet performance specifications.
Product Advantages:
The Spinal Pedicle Screw-Rod Compression Fatigue Tester offers significant advantages for assessing the critical compressive fatigue performance of these spinal implants:
Simulates Primary Spinal Loading: Focuses on the dominant compressive forces experienced by pedicle screw-rod systems in the spine, providing highly relevant fatigue data.
Provides Crucial Fatigue Life Data: Determines the number of cycles to failure under compressive loading, a key indicator of implant longevity and resistance to fracture or subsidence.
Critical for Patient Safety: Contributes directly to ensuring the long-term mechanical integrity of the spinal construct, reducing the risk of implant failure and associated complications.
Supports Regulatory Compliance: Enables testing according to standards required by regulatory bodies (like FDA) for spinal implant assemblies.
Objective Performance Comparison: Provides a standardized method for objectively evaluating and comparing the compressive fatigue performance of different screw-rod system designs, materials, and manufacturers.
Facilitates R&D and Quality Control: An indispensable tool for developing improved implant systems and for maintaining consistent manufacturing quality.
Product Features:
A Spinal Pedicle Screw-Rod Compression Fatigue Tester is a sophisticated dynamic testing system capable of applying controlled cyclic compressive loads, often as part of a multi-axis loading system that can also apply other loads (e.g., bending, torsion) to more fully simulate complex spinal kinematics. Key features include:
A dynamic testing frame (e.g., servo-hydraulic or electrodynamic) with a high stiffness and capacity suitable for applying physiological compressive loads encountered in the spine.
A specialized fixture designed to hold the spinal pedicle screw-rod assembly in a configuration that allows for the application of cyclic compressive loads. This fixture typically involves simulated vertebral body blocks (often made from a rigid polymer or bone substitute material, or sometimes using actual bone) into which the pedicle screws are inserted, and a mechanism to connect the screws to the rod and apply axial compression.
A dynamic load cell for accurate measurement of the applied cyclic compressive force.
A displacement sensor or the testing machine's measurement system to record the axial deformation (e.g., construct shortening, screw pull-out from the simulated bone) of the system under cyclic loading.
Advanced control system capable of applying cyclic loading profiles (e.g., sinusoidal, haversine, mimicking physiological loading) at specified frequencies and load or displacement amplitudes.
A cycle counter to accurately record the total number of load cycles applied.
A data acquisition system to capture load, displacement, and cycle count data throughout the fatigue test.8
Sophisticated software for setting up complex fatigue test parameters, real-time monitoring of test progress, detecting sample failure (e.g., screw fracture, rod fracture, excessive deformation), and analyzing fatigue data (e.g., creating S-N curves, evaluating stiffness and deformation over cycles).9
An environmental chamber or fluid bath designed to enclose the test setup, capable of maintaining physiological temperature (e.g., 37°C) and holding a simulated body fluid (e.g., saline solution) to replicate the in vivo environment.
Safety features such as overload protection, emergency stops, and protective enclosures.
Technical Parameters:
Dynamic Load Capacity (Compression): (e.g., typically ranging from ±5 kN to ±50 kN or more, reflecting expected compressive loads in the spine)
Frequency Range: (e.g., up to 10 Hz, 20 Hz, or higher, as specified by the relevant testing standard, e.g., ASTM F1717. typically 5 Hz)
Load Control Accuracy: (e.g., ±1% of set load or better)
Displacement Control Accuracy: (e.g., ±1% of set displacement or better)
Type of Loading: (Axial Compression fatigue, often combined with bending as per standards like ASTM F1717 for simulating different spinal segments)
Maximum Number of Cycles: (Designed for long-term testing, e.g., up to 5 million or 10 million cycles as per standards like ASTM F1717 and F2706)
Actuator Stroke: (Sufficient to apply required displacements under cyclic compression)
Environmental Chamber/Fluid Bath Temperature Range: (e.g., Ambient to 40°C or higher, with precise control around 37°C)
Environmental Chamber/Fluid Bath Temperature Accuracy: (e.g., ±1°C or ±0.5°C)
Sample Size Capacity: (Able to accommodate various pedicle screw diameters, lengths, rod diameters, and construct configurations)
Power Supply: (e.g., AC 220V or 380V, 50/60 Hz, potentially with a hydraulic power unit if servo-hydraulic)
Leave Message Get Price